Metal Roof Inspections Hot Wells TX
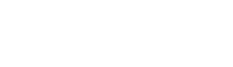
Metal Roof Inspections Hot Wells
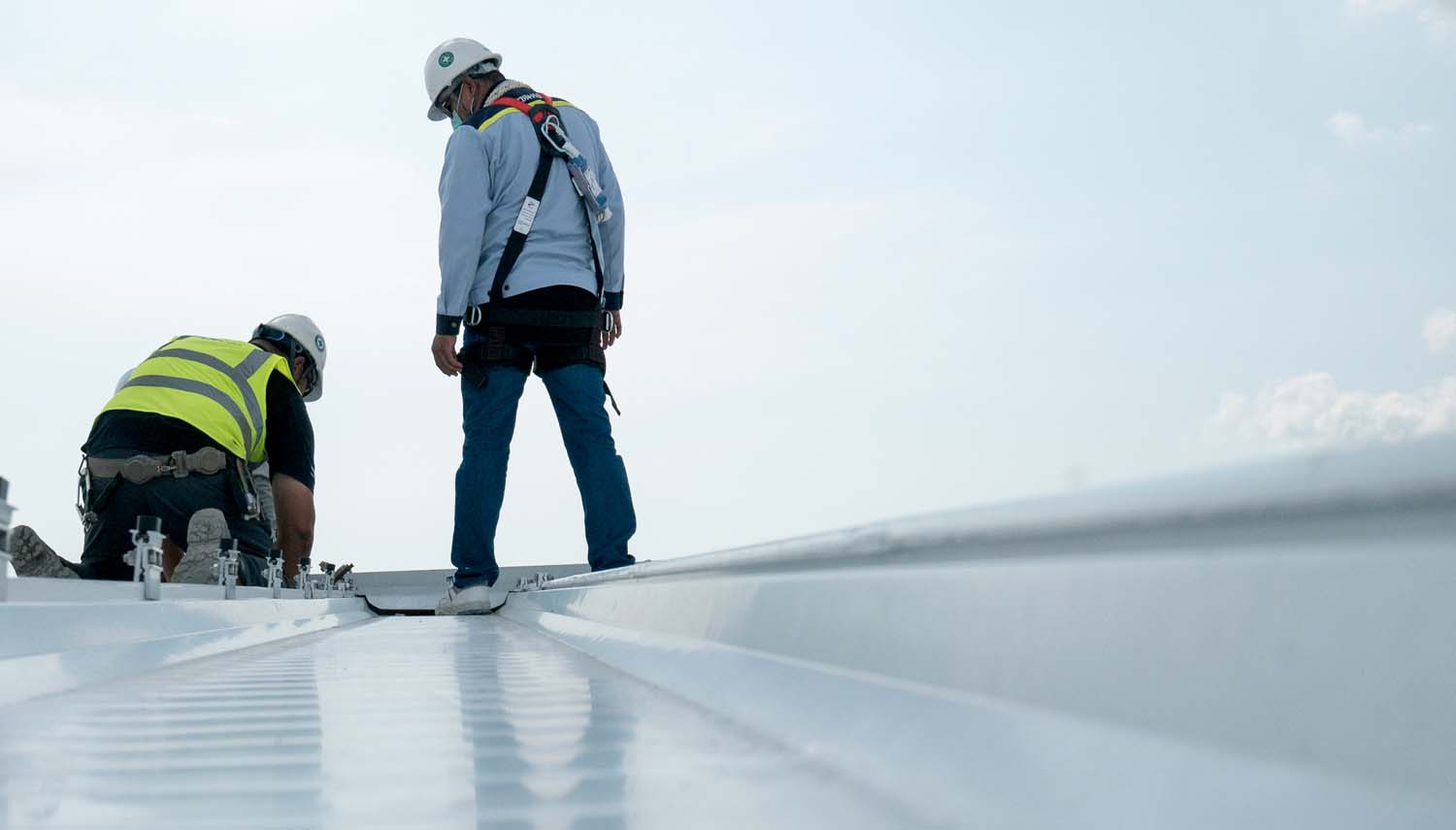
The Importance of Metal Roof Inspections for Hot Wells, TX
When it comes to metal roofs, there are two reasons why regular inspections are necessary.
First of all, these types of roofs tend to be exceptionally sturdy and durable. In addition, they can be used in many different environments, which means that they must stand up to the hazards of whatever weather is prevalent in an area. However, when it comes time for metal roof inspections, damage may not always be easy to find because these structures are often built with certain things like corrosion resistance or hail resistance in mind.
Sometimes problems aren’t apparent at first glance, so thorough searches need to be conducted regularly by professionals who know where to look for potential issues before they become significant problems. Damage could also occur due to manufacturing errors, so building owners should never think that they are out of the woods just because a reputable company has installed their roof if they never have inspections conducted.
The second reason that metal roofs need to be inspected regularly is due to their long lifespan. With proper maintenance, these types of roofs can last for decades with relatively minor wear and tear on them, making it easy to forget about having an inspection conducted once in a while. However, even when a building owner is diligent about conducting reviews, problems may go unnoticed until they become severe enough to disturb the entire structure’s integrity.
This could cost thousands of dollars in repairs instead of just hundreds or even tens of dollars for regular upkeep.
Metal Panel Roof Seams Near Hot Wells TX
There are three different types of metal roof seams – exposed, concealed, and factory-made.
Exposed Seams – Exposed seams are designed to create a durable seal between panels without an obvious cross-piece. These seams come in semi-rigid and snap-lock varieties, with snap locks being more secure but not as flexible as semi-rigid, making them useful only for flat roofs instead of pitched roofs. The pans connecting at exposed seams should overlap by a minimum of 1 inch for optimum weather protection.
Concealed Seams – Concealed seams are recommended for use on low-slope roofs. They are usually not as sturdy as exposed seams, so they are only recommended for areas where the roof will have little or no movement. This seam requires a small vertical lip at the top and bottom of each panel to overlap, preventing moisture from seeping into the structure.
Factory Made Seams – Factory-made seams are suitable for larger structures that need seams that run the entire length of metal panels, including valleys, hips, ridges, and rakes. These types of seams can be created by using either lapped, interlocking, or double interlocking connections. Lapped connections require both pieces to overlap, while interlocking assemblies allow them to be overlapped up to 1/3 of their overall length before they are attached to the supporting structure. Double interlocking connections require both pieces to overlap by 2/3 of their overall length.
These three seams must be inspected regularly to ensure that they remain strong enough to protect against water damage and other problems such as; leaks, rust, corrosion, and rot. If any of these problems are found, they should be fixed promptly before irreparable damage.
Metal Panel Roofing Penetrations
Penetrations into the roof of any structure are potential sites for leaks. That is especially true with metal roofs due to their large surface area, making even small openings problematic. Therefore, penetrations should always be inspected regularly, and any problems rectified immediately.
Standard penetrations include vents, pipes, fans, skylights, chimneys, and attic hatches.
Each type of penetration requires different types of maintenance depending on their purpose or function, which means that they can’t all be treated equally. For example, in Metal panel roofing penetration, roof vents are critical to inspect since they allow for the introduction of fresh air. However, if installed vertically instead of horizontally, they can create small leaks that go undetected until severe enough to cause damage.
Pipes should also be inspected regularly for any signs of deterioration, rust, or corrosion, which can cause cracks and other problems.
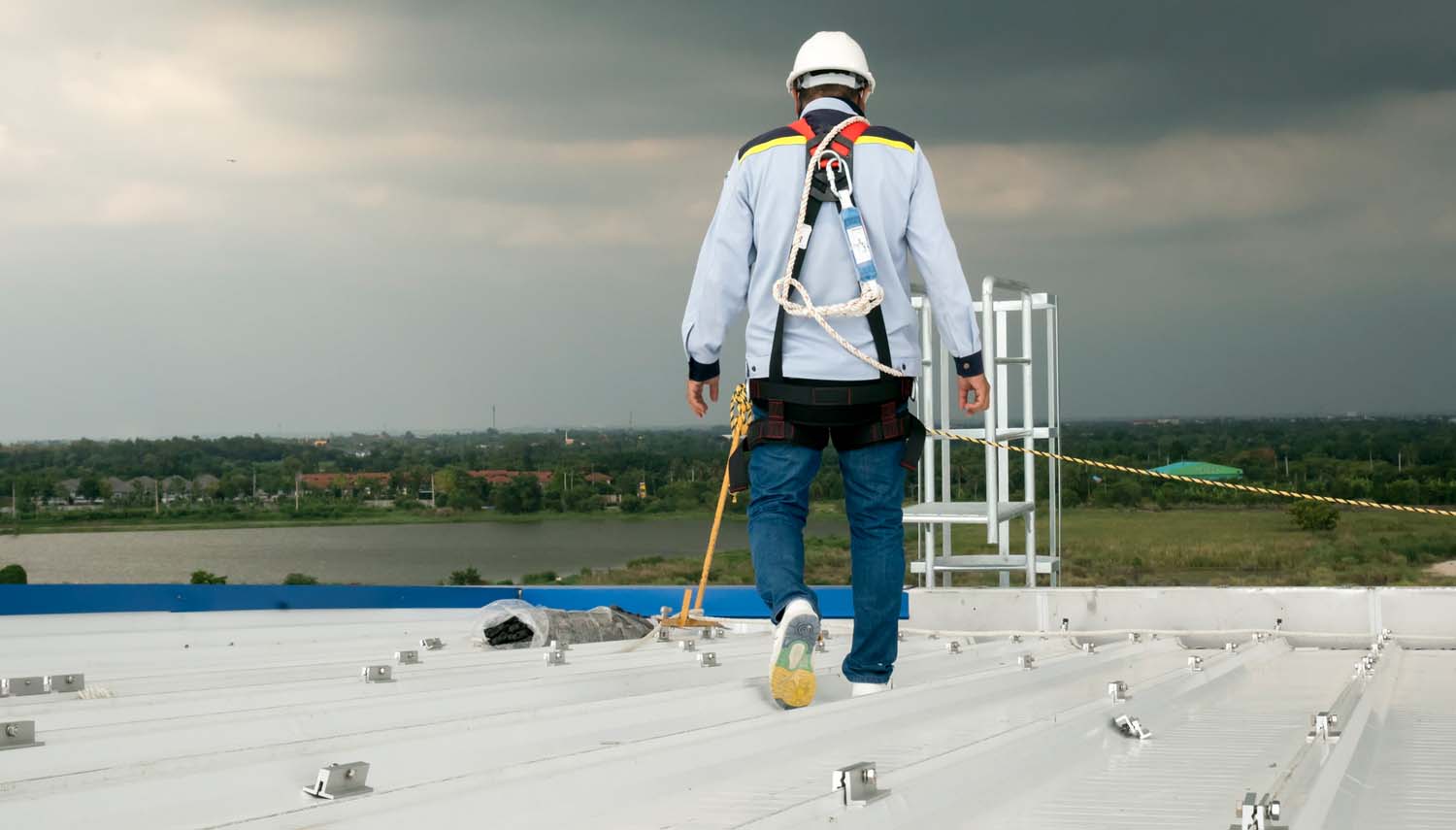
Metal Roofing Inspection Checklist for Hot Wells Texas
Metal roofing should be checked regularly to ensure that it is in good condition and able to do its job of protecting the structure. Roofers usually recommend inspecting metal roofs at least twice a year, but it’s also possible to hire a professional inspector who can conduct thorough inspections whenever necessary. Therefore, an inspection checklist is essential.
It should always be used to identify any problems before they become severe enough to cause significant damage, costing thousands of dollars instead of just hundreds.
The inspection checklist consists of;
Roof Structure – This section is concerned with the structural integrity of the roofing system, including components like trusses, support members, beams, joists, and rafters exposed to forces coming from the exterior. These parts should be checked for any signs of damage or corrosion, leading to significant problems if left unchecked.
Exposure – The exposure section includes essential items but is more related to maintenance issues than any significant damage. They have but are not limited to clearances to combustibles, ventilation, and drainage. These exposure factors should be checked regularly but only require inspections during significant renovations or when repairs are needed.
Metal Roofing Systems – Connections, seams, and penetrations are the main concern for this section of the inspection checklist. All metal roofs need regular maintenance to remain strong enough to protect against leaks and other issues. That means that the different types of connections between panels, seams, and penetrations must be inspected regularly using corrosion inhibitors to ensure they remain free from rust.
Roof Coverings – The roof covering is another vital section on the checklist because it covers all the possible sources of leaks, including but not limited to shingles, tiles, membranes, sealants, and adhesives. These components should be checked for signs of damage or wear, which can expose metal roofs to moisture in places where they might not protect against damage, like around holes made by fallen objects like branches.
How to Know You Need a Metal Roof Inspection
When you need a metal roof inspection, you see any of them for signs of deterioration or rust around your metal roofs. Unfortunately, you can’t inspect yourself as it requires special tools and equipment to check the different parts of the structure under the panels.
Suppose you notice any leaks, stains on ceilings, bubbling paint or tiles, peeling sealants. In that case, you should call a professional inspector who will help prevent severe damage from occurring to your property. Always inspect your roof before winter, as that’s usually when problems start to show themselves.
What Causes Problems with Metal Roof Inspections
It might be difficult to tell what causes a problem with metal roof inspections because there are so many different materials used in construction these days, but if there is any rust, corrosion, or wear and tear. The problem is most likely to be caused by exposure to moisture.
Metal roofs are designed to protect against damage due to rain, but if there are holes in the structure of the roofing system which allow water inside, there can be significant problems even with a metal roof. When inspecting your roof, make sure you check all connections between panels for signs of leaks like rust around seams and penetrations.
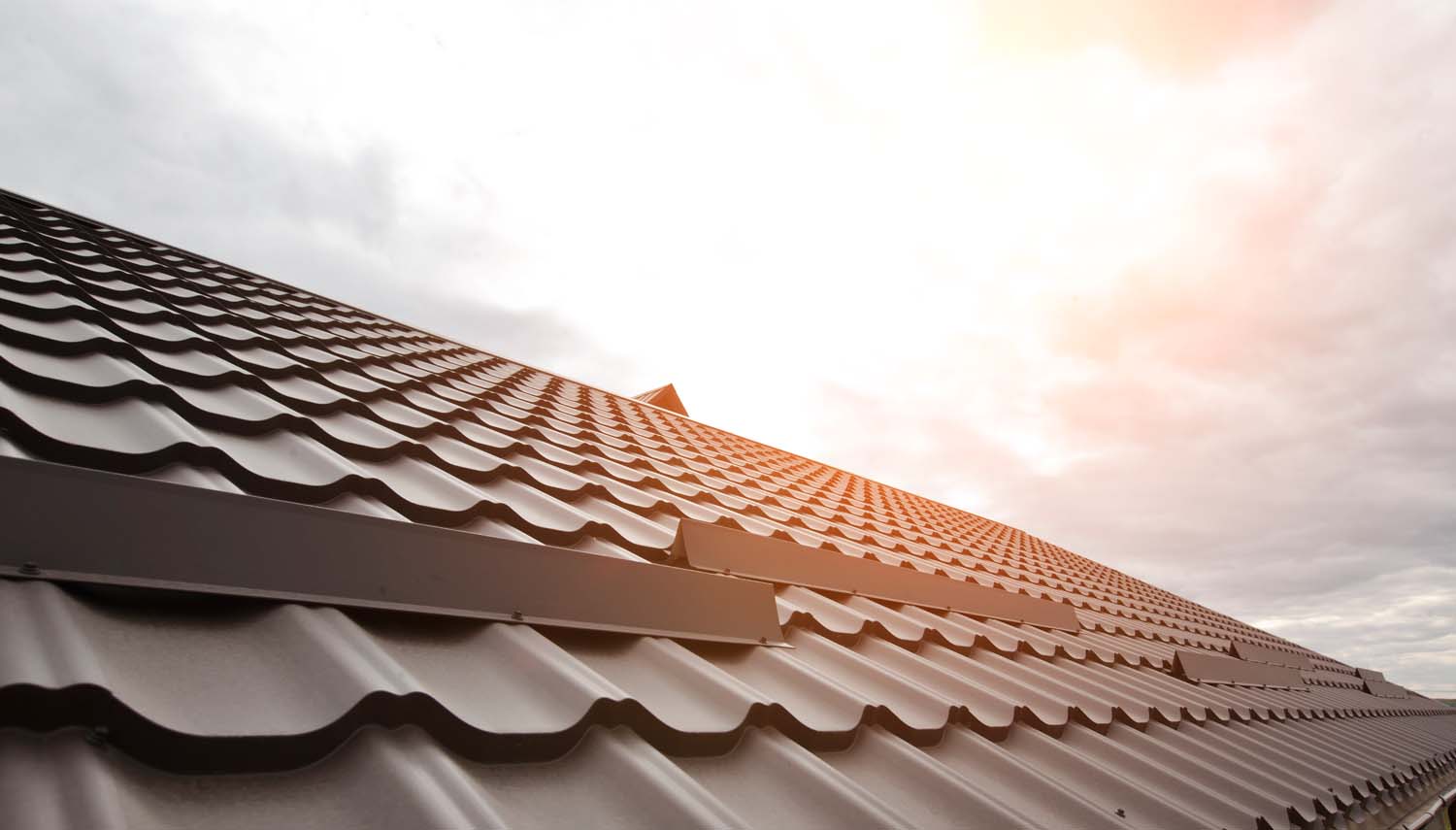
What is Involved with Metal Roof Inspections?
When inspecting your metal roof, you must look at each component separately so that any issues with each section of the metal roofing system can be identified easily. In addition, the different areas need examining carefully because they’re not always connected by something as simple as a common source of leakage.
Inspections usually start from the top by checking the roof coverings that protect against damage from sunlight and rainwater.
You should check tiles, shingles, or an equivalent to ensure they’re all in place and not damaged or missing. Next, you move down to the eaves. The edge of the roof section meets other parts like walls and guttering. It’s essential to check for correct ventilation and drainage so that water doesn’t build up around these areas and potentially cause leaks over time.
Finally, you get down into the attic spaces underneath metal roofs where there might be storage space or just space if no storage is present at all. Still, this area needs to be checked for signs of damage or leaks that could have caused significant damage to the rafters, frame, and insulation.
In conclusion, metal roof inspections are critical to carrying out regularly on metal roofs to prevent leaks and the problems that come with them. If you’re worried about your roof, then give us a call; we’ll be happy to send someone over to inspect for you.
Contact Sky Roofing Construction & Remodeling for Metal Roof Inspections in San Antonio
A roof inspection will reveal if your roof is in need of repairs or replacement. When you need a metal roof inspection in Hot Wells Texas, contact a trusted roofing contractor in San Antonio, TX, like Sky Roofing Construction & Remodeling. Sky Roofing Construction & Remodeling specializes in residential roofing. They also provide metal roof repairs, roofing inspections, and attic venting. The team will provide you with an accurate quote and will inspect your entire roof for damage or defects. A metal roof inspection will help you catch the problem before it becomes too severe. Call Sky Roofing Construction & Remodeling at (210) 942-9797.
To learn more about metal roof inspections and other services that we provide, click here.
Quality workmanship done right the first time
Contact Us
Address
415 Balcones Heights Rd.
San Antonio, TX 78201
Contact@SkyRoofingConstructiontx.com
Call Us
(210) 942-9797